Should we continue to use pegs as semi-permanent anchors, or is it time to retire them from active service?
Bolt Products is a manufacturer of rock climbing anchors, based in Germany. The owner, James Titt, has a strong traditional climbing background, cutting his teeth on the sea cliffs of Britain's south coast. As a manufacturer, he has looked into the feasibility of producing stainless steel pegs to be used for long lasting in situ placements. After doing a great deal of testing and research, he sent the BMC Technical Committee the following report:
“There are EN and UIAA standards for pegs. These set out the minimum strength and performance requirements for the design, but in no way indicate how strong a peg will be when placed in rock. Finding that only limited research appeared to have been done into how well pegs held when placed in rock, I decided to do my own testing.
Load testing results
Tests were done in vertical cracks, pulling straight out, in soft limestone. These reflect pretty much the worst placements that can be expected. Also, tests were done in horizontal cracks in hard granite, this time pulling downwards. In contrast, these are about the best placements that can be imagined.
The test results ranged from a worrying 2kN (about as strong as the smallest size RP) up to a very reassuring 31.4kN (equivalent to a good bolt). The two main factors which influence the performance are the design and the material used to make the peg.
Soft Steel
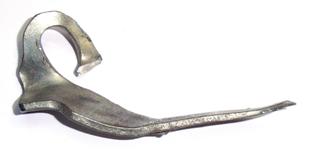
Poor to very poor performance from new and rust easily. They held equally poorly both in straight out and horizontal crack pulls, primarily because it was impossible to hammer them in any harder before they started to collapse.
The best result was 10.8kN when the eye broke (Stubai 4mm) and the lowest 2kN when a blade peg came out as we were loading the tester. This particular 5mm piton disgraced itself even further, only managing an average of 3.4kN for three pulls in the best case scenario. The manufacturer (Charlet Moser) decided to protect these from corrosion by galvanising them, perhaps overlooking the fact that zinc is one of the metals used in bearings due to its lubricating properties. In fact a bit of rust is not a bad thing, as the static coefficient of friction for granite on lightly rusted steel is 20% higher than on normal steel. The normal 5mm and 6mm blades got an average of 6.8kN in both tests, their softness allowing them to bend and slide out easily.
Hard Cast Steel
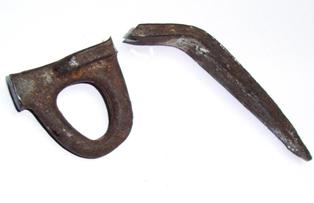
Not many, if any, on the market these days, though I tested some older ones. These were both ¼" Lost Arrow /King Pin designs, one from Cassin and the other unbranded but appeared identical. Both had good holding power, at least good enough to break, the eye of the Cassin letting go at 18.3kN and the other losing its eye completely at 21.7kN. These averaged 16.3kN on straight out tests.
Chrome-molybdenum Steel
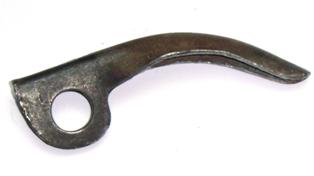
As good as it gets perfomance wise, but stress cracks can appear spontaneously even after years of good service, particularly in the bent sheet types.
Generations of climbers have relied on Yvon Chouinard's finest and a 5/16" Lost Arrow up to its eye in a horizontal granite crack certainly is a fine thing. It only came out when the rock under it started to break up and averaged 31.4kN. In the direct pull tests it was doing well at 19kN when the crack failed totally and certainly would have been much better in stronger rock.
Nothing wrong with Clog either. 30.8kN for a 5/8" channel surprised even me, though it looked rather sad afterwards and repeat tests were not possible. Its soft rock performance was relatively poor (10.8kN) as it tended to cut into the rock due to the thin material and never really took up well. The 1/8" Clog knife blade, a fairly short and wide blade compared with the shapes on the market today, was a pleasant surprise. Despite its small size it managed 12.3kN straight out and 13.8kN in the horizontal crack.
Stainless Steel
Good holding power, almost as good as chrome-molybdenum. I tried a few designs of these, conventional AISI316 6mm blades held 13.4kN straight out but tended to collapse on hammering in. The same design but from a specially hardened material held 16.8kN in this direction as we could hit it in further. These two were good performers in the horizontal, the soft getting a reasonable 24.3kN and its hard buddy 26.8kN. The two welded rod designs I tried were a complete contrast, the 6mm ones being poor with 8.4kN and 10.8kN in the two directions whereas the 8mm versions held 13.4kN and 29.2kN.
Stainless steel pitons could suffer from stress corrosion cracking near the sea. With the right alloy this can be eliminated, but at a price (€30,000 per ton)
Titanium
Depending on the alloy used performance can be similar to soft steel or up to the level of stainless steel. We only had a few knife blades to test, acquired on an expedition decades ago, and before you ask, they are not from USHBA. These proved to be astoundingly hard and one can only wonder from which part of the Russian space program the material came from.
In the straight-out pull these averaged 12kN, which was a good result considering we only got them about 2.5cm in. The flat eye design prevented us from testing in the horizontal crack. The sheer cost makes these a non-starter, the raw material costs alone of this little buddy being over €20.
Some Myths Dispelled
Myth 1: Soft steel pitons are for permanent placements. Truthfully this should be "soft steel pitons WILL become permanent", because they can be almost impossible to remove by hammer once placed, and certainly too mangled to use again.
Myth 2: Soft steel pitons mould themselves to the crack and hold better. Of course they mould themselves, but this doesn’t help them stay in. Once the initial friction is overcome they pull out under very little force. In all tests the soft steel pitons were consistently the poorest by a considerable margin, bent or not. In summary, soft steel pegs can be hard to remove, but nearly always have poor holding power!
Myth 3: You drive a piton in until the pitch of the ringing stops rising and then stop. All the pitons tested had different pitches of ringing, angles making a lovely sound even when not in a crack. Stopping driving early, when the pitch appeared to be at its highest, gave easy to remove pitons. What was considered good turned out to be unable to even hold the initial weight of the test rig. The maximum pull-out resistance was achieved when pegs were "beaten to death"; either because we just couldn’t hit them any harder or they started to collapse. Of course one's ability to hear when the ringing stops rising could be age related anyway; beware of old men’s pitons!
Myth 4: Titanium is light, strong and corrosion resistant. Pure titanium is in fact quite weak and soft, ASTM grade 1 having a tensile strength of only 240N/mm². (ASTM 1018 mild steel is 440N/mm² ). Alloyed with aluminium and vanadium (grade 5 for instance) gives the highest tensile strength of 896N/mm², about the same as cold worked stainless steel and chrome-molybdenum. Unfortunately in this condition it is prone to stress corrosion cracking in the presence of salt so for sea cliffs one needs to add palladium, ruthenium or possibly nickel. A good choice for pitons would be something like grade 27, a titanium/aluminium/vanadium/ruthenium alloy. Unfortunately this costs over €300,000 per ton for rolled material.
In situ pegs: Are they any good or not?
If you've been around for a long time and have an encyclopaedic knowledge of piton manufacturers you have some chance of identifying what you are clipping into, otherwise it is going to be pot luck whether it was produced from steel rejected by an Italian car company or the best the U.S (and British) steel industry could produce. Just looking at the head tells you little about the rest. In the picture below, the eyes look the same, but the top peg held 18.3kN, the lower peg 4.2kN!
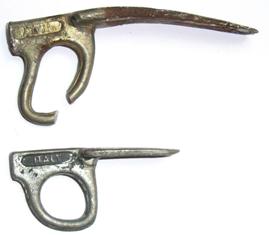
Rock erosion is a major factor; most who have climbed at Portland will be aware of the sticking out staples, which show an alarming rate of erosion of the cliff face, perhaps at the rate of 0.5mm per year. Naturally enough a piton in a crack eroding at this rate is going to be useless in a very short time. Exactly how short is hard to say but it should not be overlooked that friction forces only work at an atomic level. One of the pitons in my tests was removed from an abseil point by hand! It doesn't matter what sort of rock it is, that only affects the speed at which the erosion occurs.
All cliffs are moving, some slowly, some quickly. The cracks are there to prove it! Places like Swanage are moving quickly, one of my earliest first ascents there used a knife blade peg, later that year a Moac, and a few years later the entire buttress was gone. What use would a corrosion resistant peg be in this situation? Freezing is another potential problem, either opening the crack or forcing the piton out, with reports from the U.S and the Alps of pitons being loosened by this type of action.
Conclusions
The result of producing nice corrosion resistant pitons is that climbers may blindly trust them with potentially fatal results.
Climbers from previous generations rightly distrust in situ pegs, rusting or not, and anyway usually have a healthy aversion to falling off! The modern sport and indoor climbing generation may tend to see shiny and think strong with the inevitable consequences.
A peg can only be trusted on the day it was placed. Only the climber who placed it can give an opinion on its reliability, anything else is only a guess.
My feeling is that to put corrosion resistant pegs on the market for permanent placements would be irresponsible and other solutions need to be found.
The future for pegs
The current situation of leaving pegs in place until they have rusted away or broken leaving no alternative placement is obviously not the ideal way forward and there are a number of possibilities:
Regular replacement and inspection: perhaps removal and replacement (with chrome-molydenum steel) on say a yearly basis would make things safer but who is going to volunteer, and how does Joe Climber know it has been done?
Replace pegs with bolts: this is what is done in much of Europe, and in some ways is the obvious solution. In traditionally bolt-free areas the majority of climbers would be firmly against this though.
Drilled nut placements/threads: To my way of thinking no different to bolting, either one is using what is available or one is altering the rock to suit oneself. Hardly the British trad ethic!
Remove/do not replace pegs: That is, the routes become peg free. Obviously this is going to put the grade up on a lot of routes, or even make them unprotectable. This is in effect what is happening anyway though, as the old pegs become untrustworthy.
Return to the ethic where pitons are be placed on lead/abseil and are removed afterwards: The routes would have to be re-graded accordingly and naturally the placements will become damaged over the years and perhaps even unusable. Creative removal to leave nut placements is surely no different to drilled nut placements, only slower.
View of the BMC Technical Committee
It is should be recognised that the results and conclusions of this report are the work of James Titt, and that any test results have not been verified by the BMC Technical Committee.
It is immediately obvious that a great deal of work and thought has gone into this report. The conclusions, based on the test results, cannot be argued with. Many climbers held out great hopes that a manufacturer would produce stainless steel pegs for semi-permanent placements. This report now makes this appear extremely unlikely, and raises the dilemma of what we do in the future with pegs. This is a question for climbers at large to decide on, potentially with differences of opinion between different climbing areas.
The view of the Technical Committee, based on earlier work and taking this report into account, is that pegs should be considered as leader placed protection in the same way as nuts and cams. In other words, only the person placing the peg can have any real idea about how much security it provides. Obviously this relies on individual experience and judgement to have any great accuracy. Pegs should not be relied upon for semi-permanent placements because of their inherent unreliability and variability. Where ethics allow, only bolts or chains are suitable for semi-permanent protection or anchors.
In the view of the Technical Committee it would be unwise for the BMC to provide pegs to be used as anchors for the reasons outlined above.
Related Links
UIAA Pictorial Standard 122 for Pitons
The UIAA Safety Commission develops and revises technical safety standards for mountaineering and climbing equipment.
Bolt Products
James Titt, author of the test report, runs Bolt Products.
Winner of an OutDoor Industry Award 2008 for his innovative products.
UKClimbing.com
This feature has been produced in association with UKClimbing.com
« Back